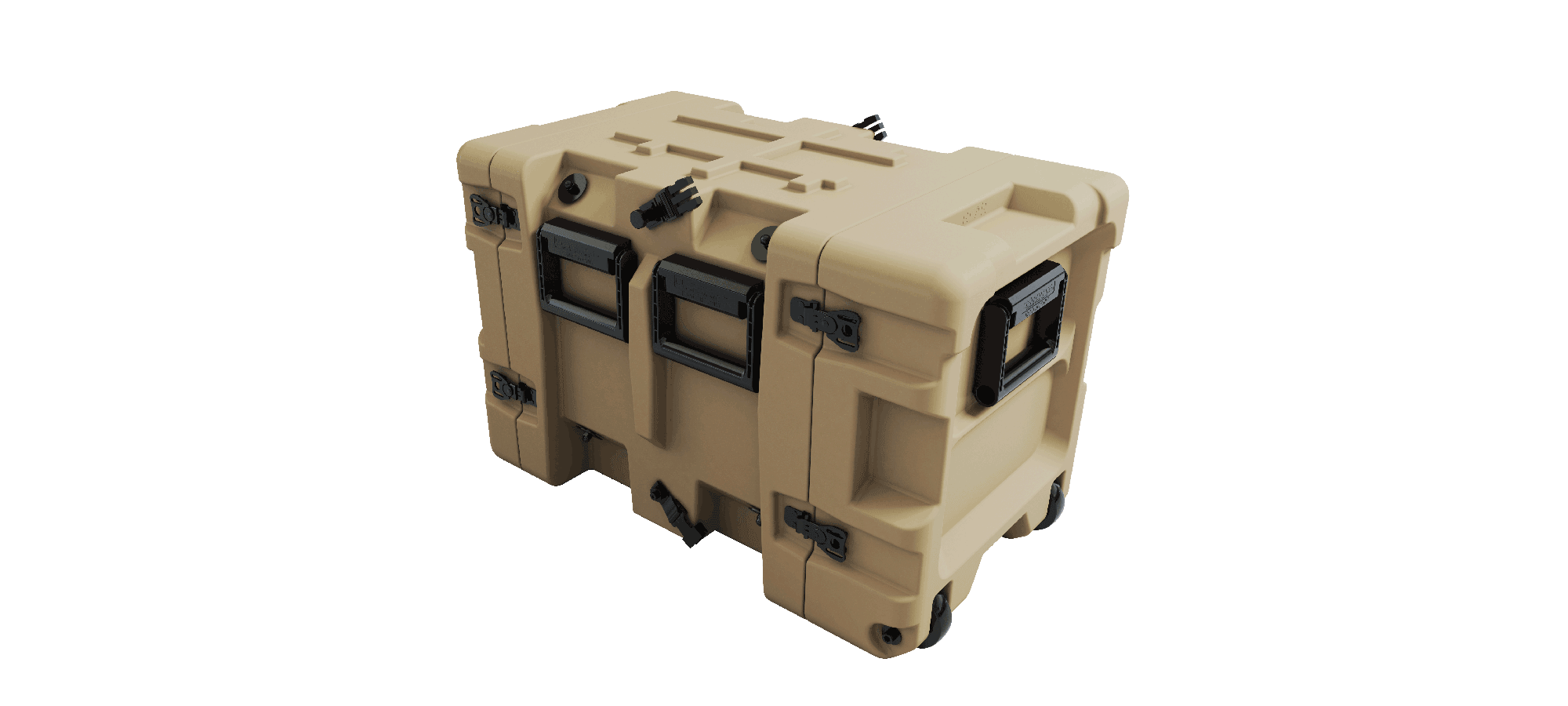
TECH NOTE: ROBORACK™ HALF-RACK CASES
ROBORACK™ HALF-RACK CASES
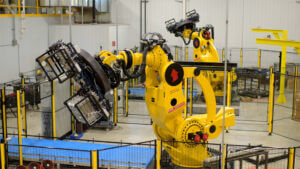
Gemstar leverages Robomold® technology to deliver lightweight cases for modern technology
Gemstar’s RoboRack™ half rack cases are the newest addition to the Stronghold® line of products manufactured with the company’s precision Robomold® technology, ensuring the highest level of protection for the most sensitive electronic components for the military industry. Gemstar’s half-rack case are military-grade, lightweight, stackable, and configurable.
Leveraging Robomold® technology
RoboRack half-rack cases utilize proprietary Robomold® manufacturing technology which is the plastics industry’s most innovative robotic rotational molding system that provides precision plastic solutions with fully automated capabilities. This one-of-a-kind technology delivers product consistency and repeatability, material control, and superior quality.
Robomold technology allows Gemstar to produce cutting-edge plastic parts, such as protective cases, with quality and consistency not previously available with conventional rotational molding. It is ideal for military applications where precision and unsurpassed repeatability are required.
High-Quality, Lightweight Protective Cases
Demand for rack-mounted cases has been increasing, particularly in the military industry where deployment of sensitive electronic equipment is vital. With the need for smaller racks increasing due to the downsizing of electronics, Gemstar opted to enter an underserved market that was occupied by only a handful of suppliers.
RoboRack half-rack cases, made of linear-low-density polyethylene (LLDPE), meet or exceed MIL-STD 810F and military Long Life Reusable Case (LLRC) standards. They feature airtight, watertight, and dust-proof protection for sensitive electronic components, rotationally-molded double walls, and thick corners for rugged, versatile, and dependable protection. Additionally, the RoboRack 5U half-rack case weighs 28% less than comparable rotomolded solutions, saving critical weight during deployment.
RoboRack protective hard cases also include recessed, heavy-duty black stainless-steel hardware, field serviceable hardware, spring-loaded handles, and tongue-and-groove construction with gaskets. An interlocking, stackable design features fully removable lids that hang on the sides, edge wheels, and an extendable pull handle. Gemstar offers the ability to customize the internal rack to meet the customer’s unique needs. The rack is composed of lightweight anodized aluminum and includes an isolastomer-dampening feature and round holes to accommodate standard clip nuts (field replaceable), delivering a payload capacity from 20-150 lbs. Please consult with a Gemstar representative or authorized reseller for proper payload rating.
Gemstar offers a broad selection of custom features, colors, and sizes. The current offering includes 5U and 7U sizes with configurable options. A key advantage is the ability to customize features inside and out to ensure proper protection for each unique application.
Robomold Technology Meets the Challenge in Military
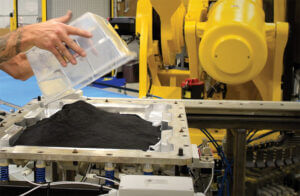
Today, the production of specialized parts and protective hard cases for the nation’s military calls for unique materials and processes that meet more stringent standards (flammability, high heat/cold tolerances, airtightness, watertightness, EMI shielding, multi-layering, etc.). Meeting these strict requirements can be challenging when using traditional molding processes such as rotational molding, thermoforming, blow molding, or injection molding.
Robomold robotic rotational molding is a leading-edge technology that meets the needs of military, OEM, and aerospace applications where tighter tolerances and precision-distributed heat and material control are required. Specifically, Robomold maintains consistent wall thickness throughout the case and optimizes strength-to-weight ratios in critical areas. For example, more material can be placed in the corners to provide added strength, while still minimizing overall weight. The product design team works to develop specific process parameters, creating a highly repeatable process, unlike the highly variable standard rotational molding process.
In the world of commercial plastic molding, robotic rotational molding offers a new approach for designing protective hard cases. This computer-controlled technology allows for precise control of multiple heating and cooling zones, customized material flow, optimized material use, increased product quality, and part traceability. It also offers instant cycle data collection, reduced cycle times, focused cycles for highly engineered resins, and the elimination of labor-intensive processes.
The core of this technology is a six-axis robot which delivers a greater degree of rotation than traditional rotational molding. Instead of using a heating oven, the robot tumbles the electrically heated mold which incorporates a multitude of separate heating zones. Direct heat applied to these zones enables plastic resin to reach its ideal processing temperature and permits manufacturers to create geometries that were previously unattainable.
Robomold also delivers a range of sustainability advantages compared to conventional rotational molding. Robotic rotational molding reduces cycle time by 25-30% with little to no scrap compared to traditional rotomolding.
LEARN MORE
To learn more about the Robomold rotational molding process, visit https://www.gemstarmfg.com/.
ABOUT GEMSTAR MANUFACTURING
Gemstar Manufacturing is an engineering-based solutions provider with 60 years of manufacturing experience and knowledge. The company is a family-owned business supported internally by long-term employees. The firm’s history is rooted in custom manufacturing and the dedication of a customer-centric organization. Gemstar’s mission is “to test the limits of plastic manufacturing and exceed the expectations of customers,” which is shown through their dedication to provide value-add solutions to customers through innovative design and technology.