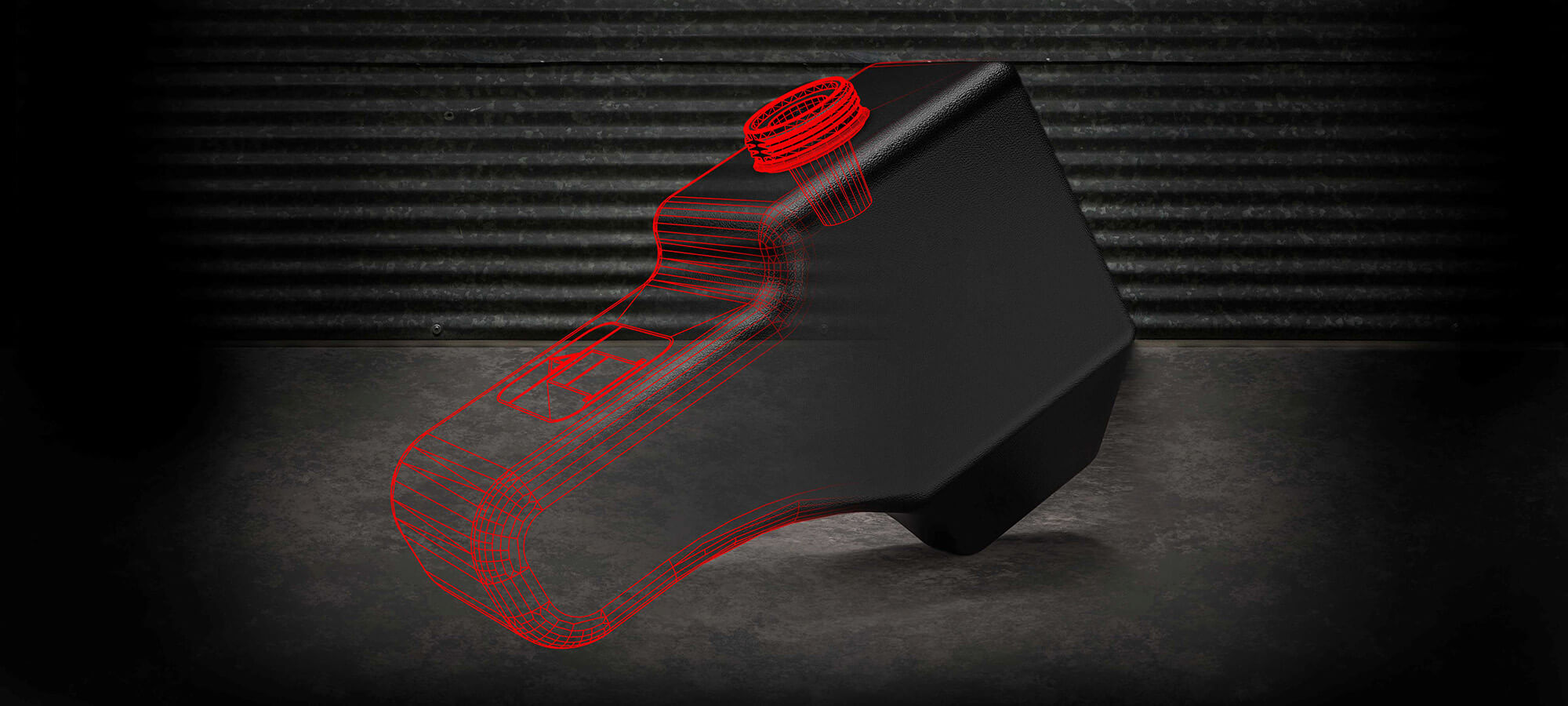
Specialized Fuel Tank Made with Robomold® Technology
GEMSTAR DEVELOPS SPECIALIZED FUEL TANK WITH EXCLUSIVE ROBOMOLD TECHNOLOGY FOR GROUNDSKEEPING EQUIPMENT MANUFACTURER
Published: November 2022 (Updated: January 2023)
Creating an epic playing experience for the golfer is what groundskeepers do. To achieve this, the groundskeeper combines their knowledge of grasses, soil, trees, brush, and other environmental elements with modern technology to create the desired playing conditions. Gemstar's Custom Part Solutions division helped design and manufacture a customized solution for such a groundskeeping equipment manufacturer in order to meet strict EPA regulations and overcome production issues.
TURNING TO A LEADER IN CUSTOM PART MANUFACTURING
Facing the challenge of increased demand for its groundskeeping machinery, the equipment manufacturer turned to Gemstar Custom Part Solutions to design and manufacture a specialized part to enhance the quality of the product while alleviating an issue caused by a shortage in the supply chain.
Based in Cannon Falls, Minnesota, just 30 minutes southeast of the Minneapolis-St. Paul metropolitan area, Gemstar is an engineering-based solutions provider with 60 years of manufacturing experience and protective packaging knowledge. Gemstar’s full-service manufacturing capabilities include industry-leading, vertically integrated manufacturing processes, a fully staffed engineering team, in-house tooling, 5-axis routing, and full-service finishing.
Utilizing several high-tech processes, including robotic rotational molding, traditional rotational molding, thermoforming, cold form bending, injection molding, and secondary fabrication, Gemstar designs, creates, and tests highly technical solutions to meet any industrial or commercial application.
Gemstar is proud to be the first manufacturer in the United States to offer robotic rotational molding. Gemstar’s proprietary Robomold® manufacturing technology provides precision plastic solutions with fully automated capabilities. Robomold technology provides product consistency and repeatability, material control, and superior quality. This technology allows Gemstar to produce cutting-edge plastic solutions, such as multi-layer products not previously available in conventional rotational molding.
LEVERAGING ROBOMOLD TECHNOLOGY
For this specific project, Gemstar’s team of design engineers recommended the use of robotic rotational molding, a leading-edge technology ideal for military, OEM, industrial, and commercial applications where precision and repeatability are essential.
Offered exclusively by Gemstar, Robomold technology creates high tolerances with precision-distributed heat and material control for consistent plastic part repeatability and optimized strength-to-weight ratios. This technology allows for unsurpassed design flexibility, including the ability to layer different compounds and coatings into finished parts where conventional rotational molding cannot satisfactorily meet evolving design requirements.
While Gemstar offers other manufacturing solutions to create custom parts, the specifications for this specific part made it the perfect candidate for Robomold technology.
“The current product the customer was using presented challenges in design,” said Kevin Paulson, Gemstar’s Director of Product. “Coupled with high demand and environmental certification, the customer was struggling to maintain acceptable production rates. Our Robomold technology allows us to optimize the design and consistently run high-quality parts.”
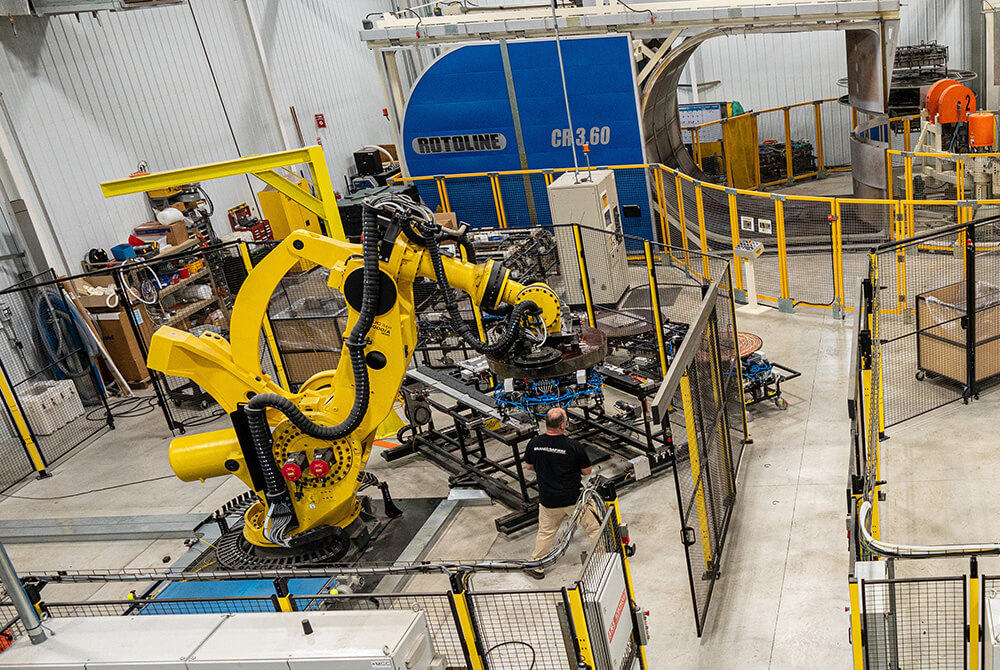
Robomold technology offered by Gemstar Manufacturing.
MEETING TWO CHALLENGES
When the customer approached Gemstar, it presented two challenges for this project:
Challenge 1: EPA's Requirements
The part that the customer needed to be designed and manufactured needed to meet strict EPA requirements. Government certification required anti-spill and anti-leak features in gas tanks. The customer needed a funnel in the filler spout to prevent fuel over-fill.
Challenge 2: Parts Production
The customer needed a reliable, U.S.-based manufacturer for this part that could consistently deliver product and meet the customer’s quality standards. This specific part was nearly impossible to mold with conventional rotational molding due to the funnel’s unique geometry inside the gas tank. Prior funnel features lacked consistent production quality that did not align with the customer’s quality standards.
DEVELOPING A PART-SPECIFIC SOLUTION
Gemstar’s Product and Engineering Team worked closely with the customer team to analyze the challenges and in doing so, created a high-quality part that meets EPA regulations.
Because Gemstar Manufacturing can provide its own tooling capabilities in-house for the Robomold manufacturing process, it was able to make nimble adjustments during the design process for the manufacture of this custom part.
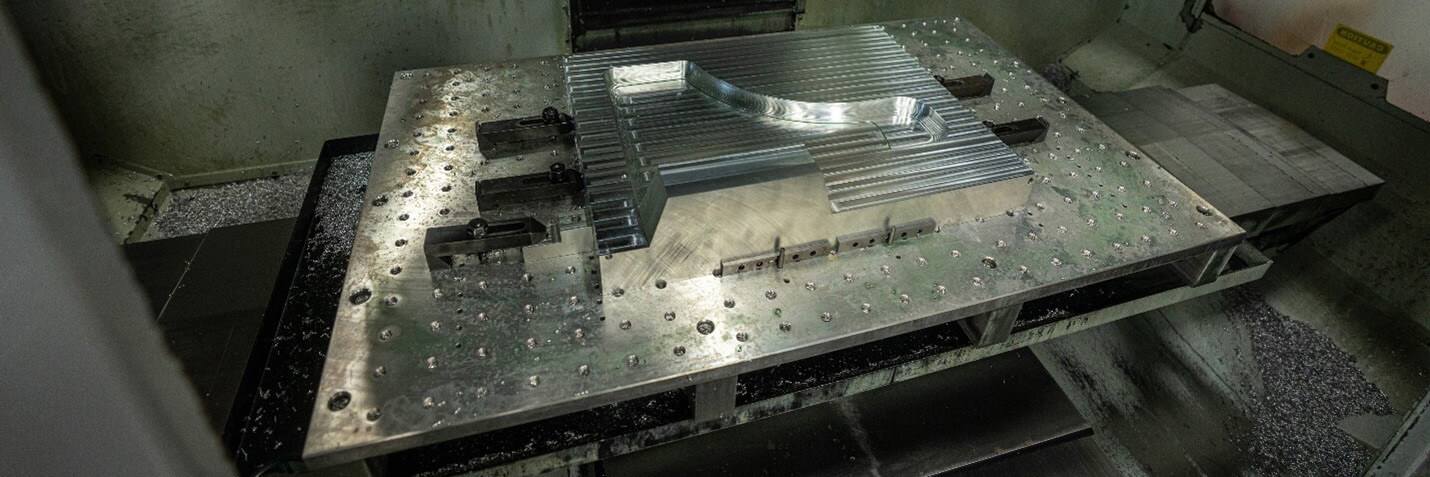
In-house tooling allows Gemstar to be more nimble in the manufacturing process.
The Gemstar engineering team engineered and built a specialty tool for this project in-house from start to finish. The tool allowed Gemstar’s Robomold robots to apply controlled and focused heat to specific areas on the funnel feature. This tool provides consistent wall thickness and geometry control as the funnel feature is near the cap thread on the gas tank.
This funnel feature breaks traditional rotational molding capabilities as the standard manufacturing process forms hollow parts – part of the funnel is inside the tank. This part was manufactured with a newly engineered industry resin, as Nylon 6 materials lacked cosmetic appeal compared to the rest of the tank.
“This project is an excellent example of how our proprietary Robomold Technology, paired with our engineering-based design solutions, put Gemstar in a unique position to solve the customer’s product challenges,” said Mark Hedin, Gemstar Vice President of Sales and Business Lead.
“In addition,” Hedin added, “our in-house testing capabilities allowed our product and engineering team to make quick and responsive adjustments during the design process. We are already working with the customer on additional improvements to this part and look forward to expanding our partnership as we grow into the future.”
By using Robomold technology, Gemstar created independent heating zones that focus the heat on the appropriate areas for optimal part quality. This process increased product quality to meet EPA regulations and decreased cycle time by 27 percent over conventional rotational molding. As part of the redesign the Gemstar team was also able to adjust the parting line to improve durability and reduce leaking issues.
"As part of the tank redesign, the parting line was moved. On the original tank, the parting line ran through the area where tank hardware such as the fuel gauge, and rollover valve were mounted. There was wall thickness variance in that area due to the parting line, and that caused some intermittent leaking issues. By moving the parting line, Gemstar was able to eliminate those issues." Explains Kevin Lumberg, Gemstar Custom Part Solutions Channel Manager.
New industry requirements will cause challenges with rotational molding, shifting suppliers to look for innovative manufacturing and design capabilities.
Printable version click here.
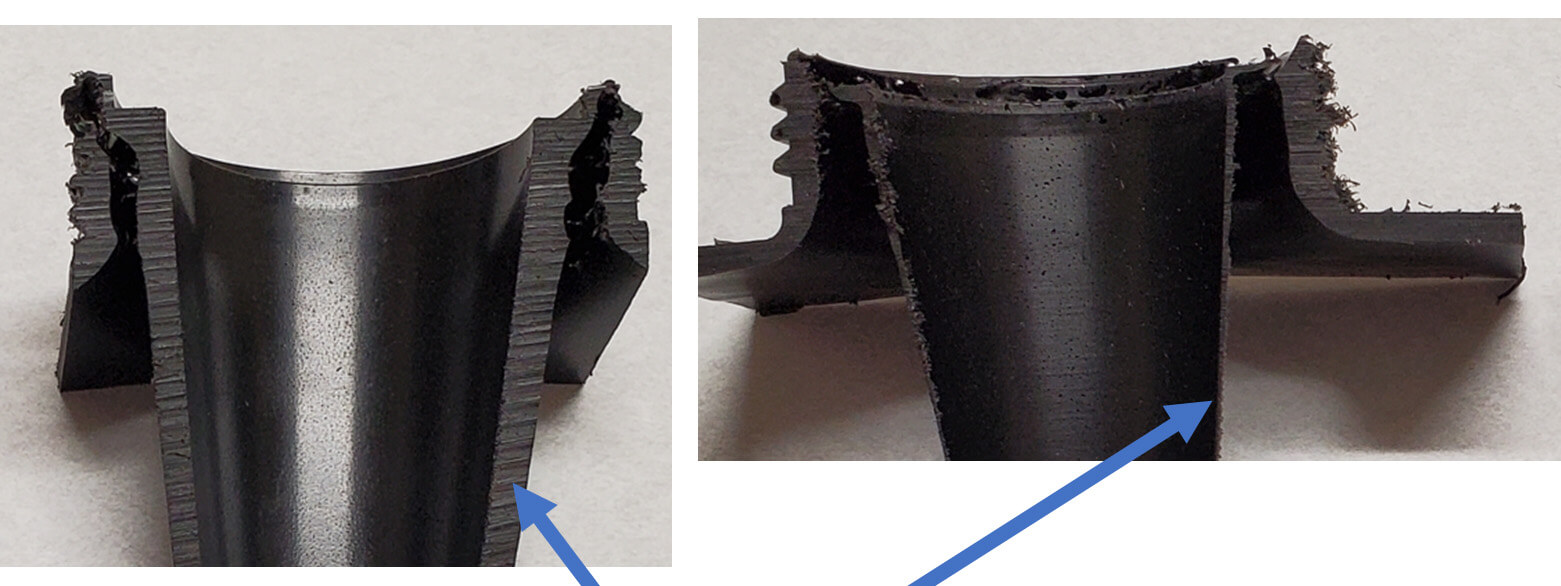
Heat flow could be focused on the appropriate area for improved material dispersion to create improved threading.
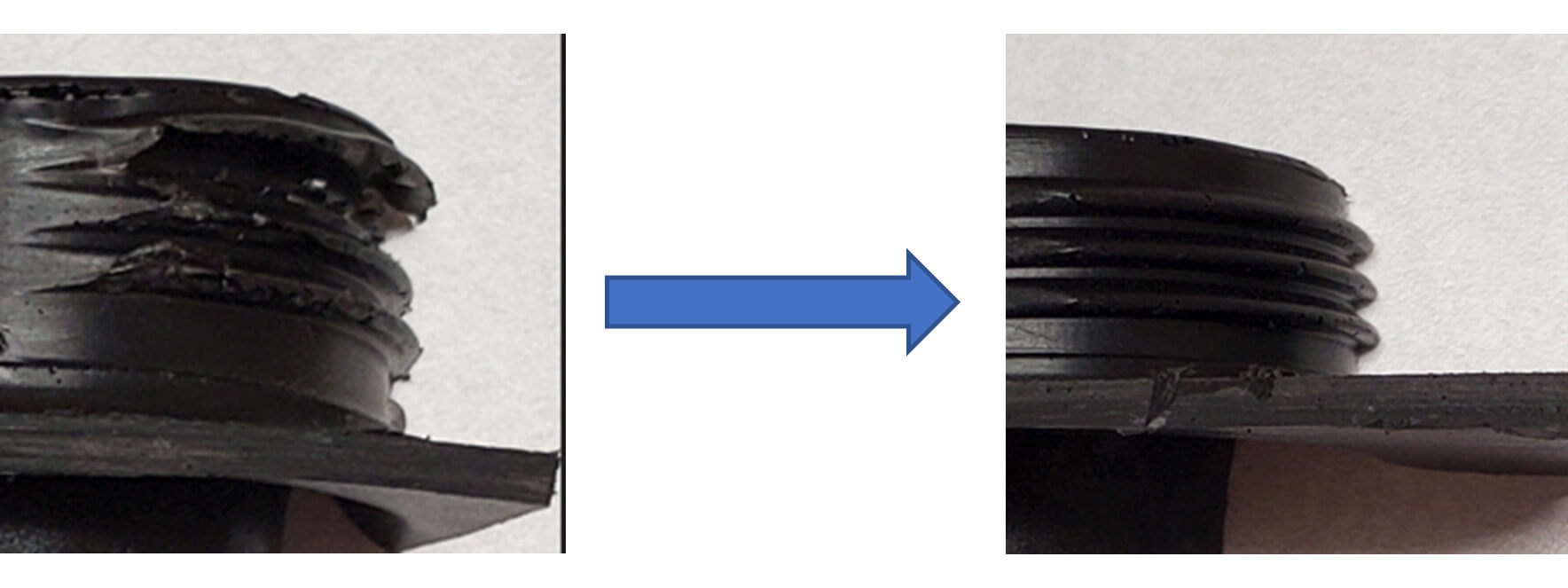
Direct heat flow also allowed for a change in wall thickness.
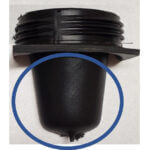
Controlled heat focus allowed for unique geometric forming not possible with conventional rotational molding.
ABOUT GEMSTAR
Gemstar Manufacturing is an engineering-based solutions provider with 60 years of manufacturing experience and knowledge. The company is a family-owned business supported internally by long-term employees. The firm’s history is rooted in custom manufacturing and the dedication of a customer-centric organization. Gemstar’s mission is “to test the limits of plastic manufacturing and exceed the expectations of customers,” which is shown through their dedication to provide value add solutions to customers through innovative design and technology.