SITUATION
Douglas Machine needed a set of plastic components for a food packaging machine to properly guide product loading into flexible packaging. The part design was fit for thermoformed ABS, a process and material appropriate for rigid, industrial plastic parts that are not a full enclosure.
COMPLICATION
The parts required tight angle tolerances, and this was further complicated by lack of structure on the part to lock the angle dimension in place, particularly after the parts were machined on Gemstar’s 5 axis router. Thermoformed parts carry inherent stress, since they are heat formed from an extruded flat piece of plastic. After forming, the material can still have a tendency to flex back towards that original flat sheet, especially when machining removes some of the originally formed material.
A standard thermoformed tool design didn’t do the job. The parts off of standard male and female tools varied beyond what was acceptable.
SOLUTION
The parts required tight angle tolerances, and this was further complicated by lack of structure on the part to lock the angle dimension in place, particularly after the parts were machined on Gemstar’s 5 axis router. Thermoformed parts carry inherent stress, since they are heat formed from an extruded flat piece of plastic. After forming, the material can still have a tendency to flex back towards that original flat sheet, especially when machining removes some of the originally formed material. A standard thermoformed tool design didn’t do the job. The parts off of standard male and female tools varied beyond what was acceptable.
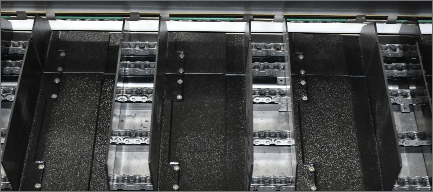
RESULTS
Gemstar’s tenacious and precise plastic solution oriented thinking allowed the team to produce precise plastic parts that met the customer’s specifications.
We were able to achieve:
- Tighter tolerances than the industry standard
- Proactive quality control procedures resulting in consistent plastic parts
- Innovative tooling construction for modular adjustments